SEGULA develops zero-waste technologies to produce sustainable carbon composites
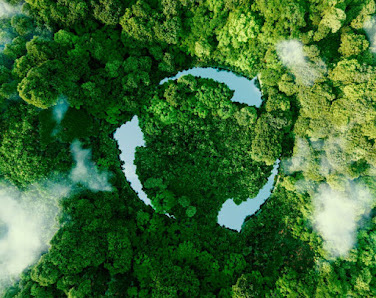
SEGULA Technologies has set up the Z-WasTEK project with the aim of developing technologies for producing sustainable #carboncomposites . Currently, parts made from composite materials have one major drawback: they are difficult to recycle and repair. The Z-WasTEK project, subsidised by the Spanish Ministry of Science and Innovation and the Basque Government, addresses this problem by combining the use of a “3R” resin (which enables materials to be reprocessed, repaired and recycled) and the development of digital programmes to define the best way of repairing parts. For #SEGULA , the project consists of two main points: firstly, the design of software for inspecting curved parts through the acquisition, management and interpretation of sensors. By performing a high-precision scan on curved parts, this software makes it possible to obtain information on points showing cracks and, after repair, to check whether the finish is correct. SEGULA has also developed a 3R #composite repair tec