Today's KNOWLEDGE Share: Shear Rate
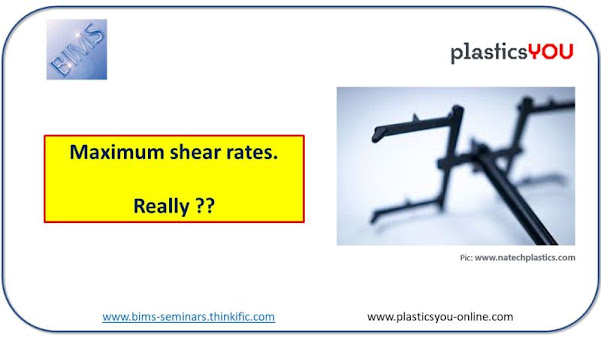
Today's KNOWLEDGE Share: Shear Rate Sorry to disappoint some of you, but there is NO such a thing as Maximum admissible Shear Rate for a material in Injection Molding. 30+ years back, Colin Austin (Moldflow founder) wanted to put a recommendation in the code documentation and, having no clear answers from suppliers ,he decided to list some values that were loosely based on a wild guess exercise. Actually an estimated typical shear rate (at some standard T) for a critical Shear Stress equal to an arbitrary fraction (abt 10%) of a Stress at break in the solid state. How wild is that ?? Shear rate does not destroy a polymer. If chains break, that is due to Shear Stress, not shear rate. If they degrade thermally, it is the result of accumulated shear-heating along the flow. In both cases, shear rates alone CANNOT resolve the risk of damaging the material. At low temperature (high viscosity hence higher stress) a lower shear rate can be more dangerous than a higher rate at a higher te