composites in Aerospace
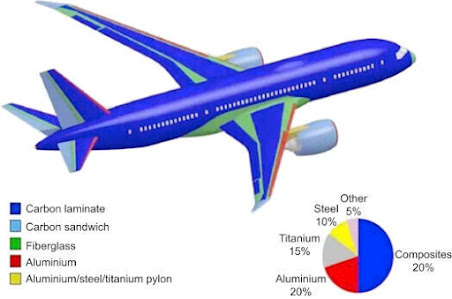
2022 Technologies in Aerospace Composite Process Composites are used in the #aerospaceindustries ; those are termed #aerospace composite. The composite materials are light in weight. The lightweight of composite structural aerospace parts helps reduce the overall weight of the aircraft, thereby leading to a better weight ratio. The structural parts manufactured using composites tend to be light in weight and possess high strength. Composites are used to make various parts of #aircraft like engine blades, interiors, and nacelles.