Today's KNOWLEDGE Share: Why do we fail so often to predict brittle failure ?
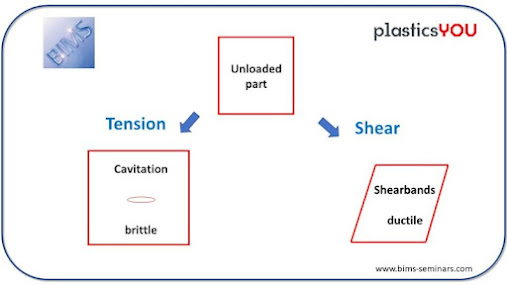
Today's KNOWLEDGE Share: Why do we fail so often to predict brittle failure ? Shear (or compression by the way) cannot promote cavitation and crack. It may however trigger Yielding and ductile failure, which we predict often correctly by looking at the equivalent Von Mises stress (a sort of average shear load) and compare to Yield. Brittle failure is initiated when our load is not trying to change the sample shape (like shear does) but rather the sample volume, more specifically in tension. If we fail to scrutinize the level of so-called "triaxiality", as described by the 3 Principal Stresses, brittle failure may go unpredicted. This is why, in our industry, we suffer from severe customer complaints or liabilities, usually related to "unexpected" brittle failure in the field. Source:Vito Leo Visit MY BLOG http://polymerguru.blogspot.com #plastics #failure #brittle